Our biggest return on investment (ROI) is the fact we had an injury-free year, a major achievement in the railroad industry. Flowfinity allows us to keep our employees safe by proactively enforcing and tracking rules with mobile technology.
A&M Railroad Reduces On-Site Injuries to Zero
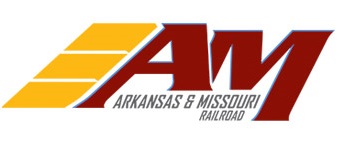
Region: Americas
Company Size: SMB
Industry: Railroad
Function: Safety Training Management
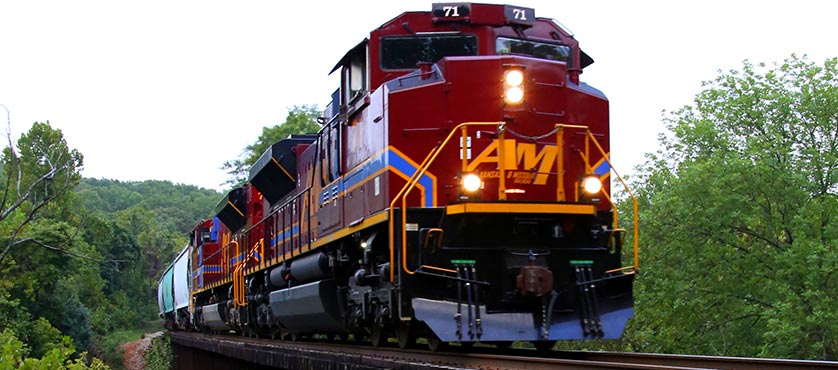
Overview
The Arkansas & Missouri Railroad (A&M) operates freight trains that carry timber, metals, and grain products, and excursion trains that take passengers through the Boston Mountains. Established in 1986, A&M collaborates with other short line and Class 1 railroads to extend their freight services to cover the U.S., Canada, and Mexico.
After noticing a customer efficiently perform inspections on iPads, A&M envisioned a new and improved safety training program with mobile technology. Management decided that having an information system in place that could distribute safety regulations, manage employee compliance with training requirements, and operate across mobile and desktop computers would be an important part of the solution. Using Flowfinity's no-programming approach, they quickly had a custom mobile solution built that met all their operational requirements for improving employee safety compliance.
In its first year of operation, the custom solution enabled A&M to achieve zero injuries for only the second time in 30 years of operations.
Results:
A&M successfully streamlined their entire safety training management and reporting process with a mobile application that achieved primary objectives of:
- Reducing reportable injuries to zero
- Improving Federal Railroad Association (FRA) compliance
- Doubling the rate of efficiency testing
- Reducing inventory costs up to $100,000 per train
- Enhancing evidence for liabilities and litigation
"Employee safety is our #1 priority, and Flowfinity enables us to provide comprehensive training and testing for rules awareness," said Ron Sparks, Director of Safety, A&M. "The FRA is very impressed with how we initiated a custom solution to enhance safety, and foresees mobile technology becoming the new industry standard."
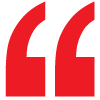
"Our biggest return on investment (ROI) is the fact we had an injury-free year, a major achievement in the railroad industry."
The Challenge
A&M is a short line railroad with trains moving at speed limits up to 49 mph and reaching steep elevations through the Ozark Mountains. Due to the inherent high risk of incidents, A&M conducts safety briefings for field staff to reinforce proper operating practices of freight trains.
Previously recorded on paper, briefings begin with an overview of safety rules pertaining to each task being performed that day, and end with efficiency testing to confirm understanding of presented material. All data was handled manually which made it slow and difficult to determine which employees received safety training, the type of training, and when it occurred.
"Information was inconsistent, unreliable, and required manual work to look up details," said Sparks. "We spent hours going through boxes of paperwork, only to end up not finding what we needed."
The challenge was to cost-effectively design and implement a system that would meet the combined requirements of federal regulators, company management, and operational staff to achieve the safety objectives.
The Solution
A&M selected Flowfinity's cloud-based, mobile business process application product to build a solution accessible on iPads, smartphones and desktop computers. The solution is used for streamlining safety briefings and enhancing emergency preparedness. Flowfinity was chosen over other solutions because of its user-friendly app interface and powerful features that allowed them to implement all workflow requirements to match railroad safety procedures.
Results
Management's vision for a better way to manage and achieve operational safety has been realised with a fully mobile-capable business process system that meets all their training and documentation requirements. With the features and flexibility of Flowfinity, the system can be enhanced at any time to meet new operational or regulatory requirements going forward.
Instant updates
A&M can now regularly deliver updated briefings through the mobile app for any change in safety regulations to further improve FRA compliance. Application updates are made instantly and across all mobile devices. Field staff can also access A&M's most up-to-date Railroad Rule Books directly on iPads, and rest assured they are following the proper safety protocols.
Improved safety record
After implementing their new system in Flowfinity, A&M successfully achieved their goal of zero FRA reportable injuries for only the second time in 30 years of operations.
"Our biggest return on investment (ROI) is the fact we had an injury-free year, a major achievement in the railroad industry," said Sparks. "Flowfinity allows us to keep our employees safe by proactively enforcing and tracking rules with mobile technology."
Doubled efficiency testing with customized safety briefings
The mobile solution A&M built enables them to custom each briefing to cover emerging industry safety trends, in addition to topics specific for tasks that day. Comprehensive testing has doubled and is performed efficiently, recorded accurately, and stored instantly onto a cloud server. With two-way data flow from a centralized database, A&M's management can quickly look up training material from all departments.
Better accountability of field staff
A&M takes advantage of Flowfinity's real-time data reporting for better accountability of staff. Following each safety briefing, efficiency test results and electronic signatures confirming acknowledgment of understanding are immediately sent to the office for recordkeeping. Date and timestamps are included, and data is summarized into tabular reports that automatically calculate how many safety briefings each person has completed.
"Flowfinity enables us to prove each crew member was trained properly before operating any trains," said Sparks. "We have proper documentation of where, when, and what type of safety training occurred. This is powerful information, especially for cases involving the FRA and legal matters."
Reduced inventory costs up to $100,000
By keeping staff safe and healthy, A&M can maintain steady operations and avoid annulled freight trains. Each time the organization halts operations, it can cost them between $10,000 to $100,000 of inventory per train.
"Our customers rely on us tremendously for inventory, as they don't have warehouses and are based on JIT (just in time) shipment," said Sparks. "We want to make sure our field staff can go home at the end of each day, and Flowfinity lets us do exactly that."
Future
A&M sees the potential of expanding their use of Flowfinity to excursion trains, which carry over 40,000 passengers per year. A mobile application would enable them to capture real-time data about how many passengers are on board, which staff members are working, and if pre-train checklists were completed before departure.
"Flowfinity would help us build a powerful solution that enhances the experience and safety of the passengers, and the accountability of the staff on board," said Sparks.
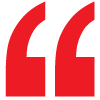
"We want to make sure our field staff can go home at the end of each day, and Flowfinity lets us do exactly that."